Quality Control
- 5-year warranty for driving part, and 1-year warranty for electronical parts and wearing parts.
- Easy inspection and maintenance for parts on forming table.
- All parts under forming table should be lubricated every four to six month with specified oil.
Mechanical Properties
DESPU-B80 paper container forming machine possesses a working table, which well separated driving part and molds, and placing driving part inside the chassis under the table. Automatic lubricant spraying system, vertical shaft driving structure, cylindrical indexing CAM mechanism and gear driving system are all equipped. Formed molds can be set on the table, easy to be cleaned and maintained. Besides, DESPU-B60 also adopts PLC, photoelectric tracking and servo feed system to control the electronical parts.
Adopts inclined frame, the cup drop rate reaches99.99%
Flat head clamp is adopted to ensure effect of feeding paper smoothly.
Paper cup bottom conveyor can adjust automatically.
Die plate, paperboard plate and cup wall plate use aluminium material, they feature of light weight, good anti rotating inertia and long service life.
Intelligent Control System
- Frames of multiple models. Easy selection and operation with clear directions.
- Easy setting for parameters. Data back-up, recovery and factory setting can be achieved. Manual setting is also available.
- Program origin and direction can be automatically set. No failure will be missed from self-Inspection system. When installing encoder’s hardware, you only need to set the software data rather than considering hardware’s installation position.
- Automatically stop at certain place and lower itself rapidly within one round. After setting, machine’s inertial running distance will be automatically measured, at least one step further than the position reached after slowdown.
- Signal in key areas can be automatically counted and recognized. Once there is any failure in forming process, the system will automatically track the signals according to the sensors, and stop the mold between two heaters.
- Cup will be automatically fetched out when failure occurs. Unexpected stop may lead to the burned-out heater and the unfirm adhesive, so heater and frame will be automatically removed.
- Intelligent temperature control for heating system. PLC and PID temperature control system are applied. Targeted temperature will be automatically set when users input the manufacturer, weight, single or double PE coated of papers. Besides, when targeted temperature changed, the production efficiency will have a change as well. Users can also customize the targeted temperature curve.
- Appearance inspection system. Cup shape and flaws inside and outside the cup can be automatically recognized and removed. With unique arithmetic method, this machine can locate the light gray stains easily and correctly. Parameters can be set and changed easily. Report in internal monitoring can also be output.
- Hardware monitoring system. PLC input, relays, contactors, PLC and touch screen, PLC and computer. PLC can timely monitor the expanded lines. When failure occurs, alarm will be sounded and the failure cause, detailed information about faulted software or hardware will be reminded. In this way, faults can be easily removed.
- Long-distance upgrading is available. When high speed Ethernet is used to connect PLC and touch screen, IP address of PLC and touch screen can be revised. Besides, long-distance upgrading can be achieved with NAT or other internet providers.
Specification
Model | DESPU-B80 |
Output | 60-80 pcs/min |
Dimension(oz) | 12-170 oz |
Application | salad bowl or large buckets |
Cup Shape | 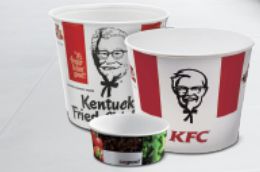 |
Paper Type | Single-coated PE/double-coated PE/PLA |
Paper Thickness | 0.3825-0.5025mm |
Cup Size | (D1)ф150-180mm (H)60-100mm (D2)ф100-160mm (h)7-12mm |
Power | 3-phase 380V、35KW |
Compressed Air | 0.6-0.8MPa,0.5m³/min |
Weight | 4500kg |
Packaging Box Size | 3200 x 1700 x 2350mm |
Cup Counting Shelf Packaging Box Size | 1230 x 720 x 1900mm |
Note: Optional Configuration ○ Standard Configuration ●
Process
Paper suction
Side heating
Folding/Sealing
Bottom feeding
Bottom heating 1
Bottom heating 2
Bottom curling
Bottom knurling
Oil dipping
Top curling 1
Top curling 2
Cup discharging